Powder Coating
Basic Principles of Powder Coating Process
Dry powder is conveyed by compressed air from the powder feeder to the gun tip where it is electro-statically charged (up to 90Kv) before it is sprayed. As the object is ground, charged powder, gets attracted to the object and get settled on its surface. The powder deposition is controlled by Powder flow, Shape of object, Voltage set on Coating Machines & Gun-operators skill. Over-sprayed powder is recovered and recycled. The coated articles are conveyed to curing oven (for curing cycle of approx. 180 – 200° C for 10 – 15 mins. Object temp. depending on formulations) for curing the powder
Salient Features of the Powder Coatings
- No primer coats are needed. Single Coat Application
- Over spray loses are greatly reduced
- Labour & energy cost are reduced
- Cleaning of Wet paint booth is eliminated. No VOC’s
- Powder is 100 % Solid
- Powders are supply ready for used and hence do not require thinning or mixing before application
- Rejection rates are low
- Plant occupies lesser space
- Cost of paint storage is reduced
- No flameproof equipment needed
- It gives better chemical & Mechanical Properties
- Performance based powder for every application
Advantages of Powder Coatings
- No runs, sags, drip
- Better edge coverage due to wrap around property
- Superior scratch resistance
- Superior chipping resistance
Advantage Powder Coating Process
- No Solvents, which means a) No objectionable odors, fumes etc. polluting the plant atmosphere b) Greatly reduced fire hazard
- Up to 98-99 % Powder utilization
- Only one coat is needed to give adequate coating thickness in the recommended range of 50-60 microns
- No mixing necessary. Ready to use as supplied. Therefore no chance of error on the part of the operator
- No primers required, material develops excellent adhesion as a result of chemical reaction that takes place during curing
- Process can be easily automated. Inexperienced personnel can become a Proficient within a short period of time
- Any powder spillage on operator’s clothes or on ground can be just brushed away or vacuum cleaned
- If prior to baking, coating found unsatisfactory, powder can be blown off and the object can be recoated
Uses on the Basis of Different Generics of Powders
Pure Epoxy Powders
Due to its Excellent Chemical & Corrosion Resistance applications are, Automobile Components, Electric Motor Covers, Switchgear Boxes, Office Equipments, Textile Machinery, Computer Parts, Glass, Home Appliances, Hospital Equipments, Toys, & Bathroom Fixtures etc.
Epoxy Polyesters Powders
For General purpose and at exterior parts were there is no prolonged exposure to direct sunlight. Schools & Office Furniture Super market Shelves, Light Fittings, Fire Extinguishers, Power Tools, Grain Storage Bins, Oil filters & Air Cleaners.
Pure Polyesters Powders
For Exterior applications due to excellent whether-ability : Coating on Aluminium Sections, Grills, Architectural Paneling, Automotive parts, Irrigation pipes & Fixtures, Outdoor furniture/Equipments & Farm Equipments.
Polyurethane Powders
Polyurethane Powder Coating is used where high Humidity Resistance, High Salt Spray Resistance, and Excellent Exterior Durability is required. It is recommended for use in exterior situations when lower film builds (Thin Film application/Fine Film) with superior Flow are particularly important.
Applications
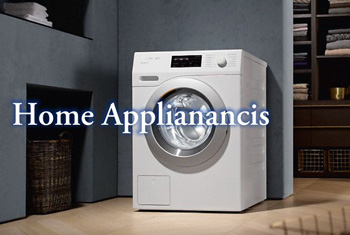
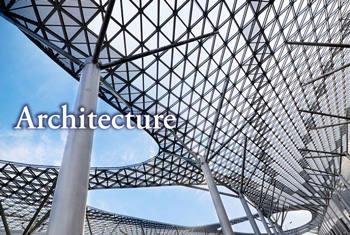
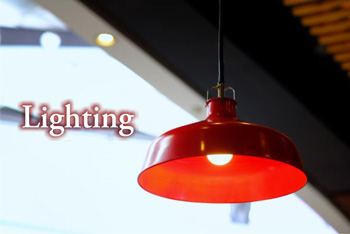
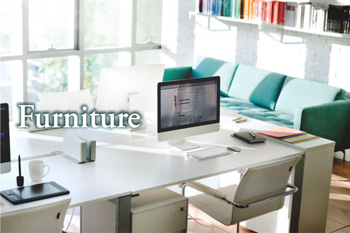
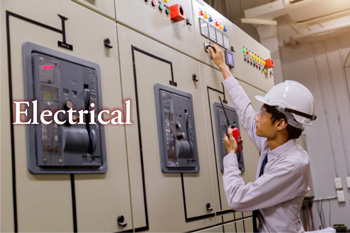
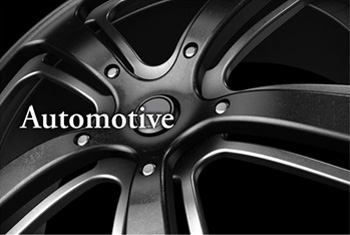
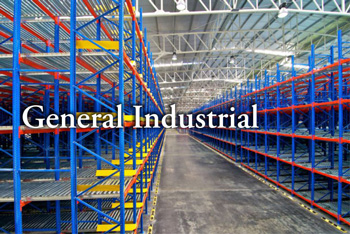
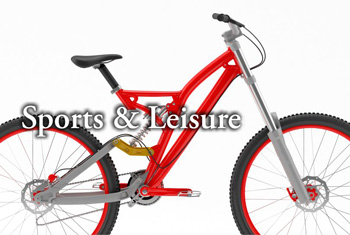
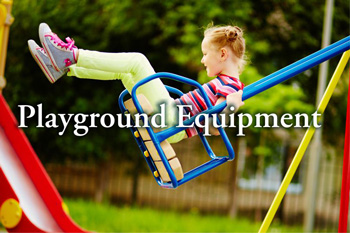
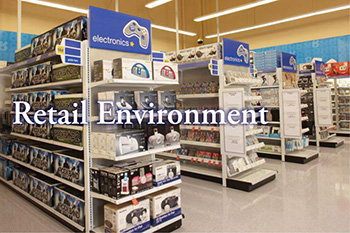